PCB 设计:业务概要
- 10年以上专业设计经验,工艺改进,完成技术支持业务。 支持主流设计工具:Allegro、Pads、Mentor Expedition
- 设计类型:高速、仿真、软硬混合、高密度、高压、高效率、射频、背板、ATE、柔性电路、软硬结合板、铝电路板等。
- 满足客户在设计、进度、成本、材料、制造工艺及其限制、可靠性、安全性等方面的专业知识。
- 以高速设计为主导,对高速板及工艺的深入研究和技术积累。
- 周密的 DFX 模拟系统,也考虑到了设计初期的生产问题。
PCB 设计:能力
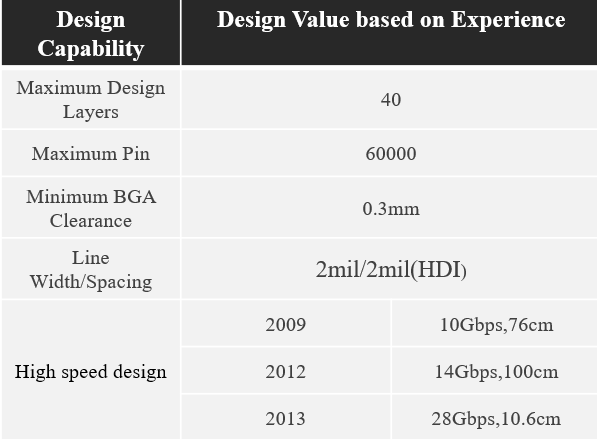
信号完整性分析(SI Simulation Analysis)
我们有完整的 SI 设计和 SI 问题的解决方案流程。根据设计和信号完整性时序的要求,前布线仿真可以设计人员选择元件,调整零件布局,规划系统时钟网络,确定关键网络的端接策略和拓扑结构。并确定关键网络的终止策略和拓扑结构。布线后仿真可以评估反射、振铃、过冲、串扰和时序等布线参数是否满足设计要求,帮助揭示潜在的 SI 问题,提高设计的可靠性。
电源完整性 (PI Simulation Analysis)
如果电网的设计有缺陷,会直接影响整个系统的稳定性。我们在大电流电网设计领域积累了大量的经验。结合前期设计中现有的仿真方法,我们可以检测早期风险,优化器件和电源模块的布局,没有。的焊盘,电容分布,保证了供电网络设计的可靠性。
可制造性设计 (DFM)
电路板、组件及其结构将在成本、效率和质量方面做出最佳选择,因为从产品规划开始就全面考虑了产品使用时,就考虑到了与生产相关的过程问题。特别是,电路板的 Layout 需要符合此选择。并在设计过程中,各环节的板面检查和修改均采用各种模拟软件和专门的检验规定,确保产品从设计到生产的良率,大大提高了产品设计的可制造性,从而达到了省时、省料、省成本的效果。